This is a log (pun intended) of my wood splitter build. Yes, Wood (pun intended) have been easier to just buy one but I wanted one that fits the way we work our wood and no one currently offers anything like it. Me and my dad use wood as our total heat sources and have done so for over 30 years now.
We currently have a self contained, fixed, horizontal homemade that Dad made and has been strengthened over the years. The other splitter is 3 point that someone else made that has been rebuilt so I've learned from these what I want. the 3 point is nice as you can lay it on the ground for the big ones.
With this splitter I want to get rid of the straining and a lot of the bending over. If you split a lot you day dream a lot about, "hey, it would be better if....." That's where a lot of these ideas came from.
Pumps and such came from P&J commercial products(1-877-775-4839. James builds and sells splitter to order and helped me a lot. He advertises here and is a top rate guy. I'd highly recommend them and tell them Kevin in Ohio send you.
Not saying this is the way everyone should do it, it just suits our needs and I'll try to give some tips along the way to help others. Here we go!
I've been planning this build for several years. Did a little research and found what size motor was needed and started keeping my eyes open for a deal. Finally this mower was listed on craigslist and snatched it up.
You'll be dealing with a vertical shaft motor as opposed to horizontal but to me, it's not a big deal. This one was extremely nice and with the advent of hydrostatic transmissions now, you can find some bigger motors on smaller mowers.
25 HP is more than I need for a 28 GPM pump but my thinking was with the way they label motors anymore, 25 HP today isn't what it used to be! Plus the fact if it wears some and the power decreases, I still have plenty to do what I want and it is not stressed
Only had 271 hours on it and got the mower for $325.00. Guy was moving and had to go. Found it on Craigslist. A big plus is you get a lot of extra stuff with a rider. I'll use this hour meter along with cables and such which will be nice.
Ready to dig in! Ideally if you had a mower like this allready you could have a bunch of spare parts for your own. I'll sell the stuff off and you can basically get most, if not all, your money back. The electric clutch on this goes for $325.00. hydros are up there and decks are easy to resell in the Spring.
Less than a hour it was down to the motor. I didn't just rip stuff off as I labeled some of the safety stuff so when I go to clean up the wiring I know what to delete....hopefully!
(Side note) ended up selling all that I didn't want for $125.00 so I have $200.00 in the power plant and extras. Could have gotten more if I waited till the Spring but wanted it out of the way.
Electric clutch was easy to get off with impact as it's just 1 bolt. The pressed on pulley was a bear! Ended up welding to bolts with the heads cut off to the outside of it. Then ran that through a 1/2" plate and tightened the nuts. Old school trick but never failed me yet! No damage to the crank and you don't beat on it that way.
As you can see I tried the standard 3 jaw puller first and it was obvious that wasn't going to get it off. put washers to get more movement. I then loosened up and put a socket on the shaft and pulled it the rest of the way off.
We currently have a self contained, fixed, horizontal homemade that Dad made and has been strengthened over the years. The other splitter is 3 point that someone else made that has been rebuilt so I've learned from these what I want. the 3 point is nice as you can lay it on the ground for the big ones.
With this splitter I want to get rid of the straining and a lot of the bending over. If you split a lot you day dream a lot about, "hey, it would be better if....." That's where a lot of these ideas came from.
Pumps and such came from P&J commercial products(1-877-775-4839. James builds and sells splitter to order and helped me a lot. He advertises here and is a top rate guy. I'd highly recommend them and tell them Kevin in Ohio send you.
Not saying this is the way everyone should do it, it just suits our needs and I'll try to give some tips along the way to help others. Here we go!
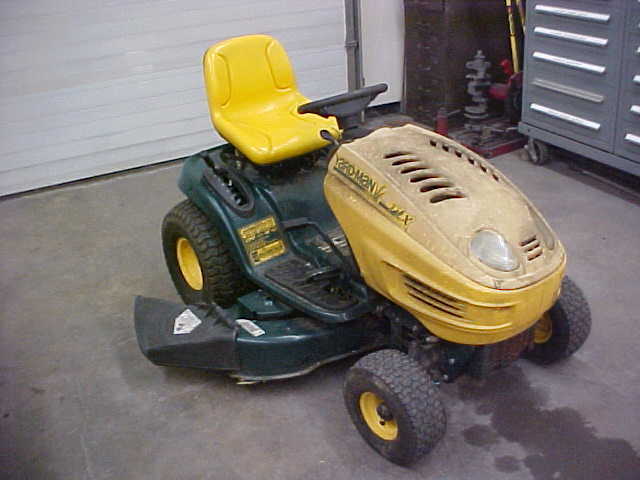
I've been planning this build for several years. Did a little research and found what size motor was needed and started keeping my eyes open for a deal. Finally this mower was listed on craigslist and snatched it up.
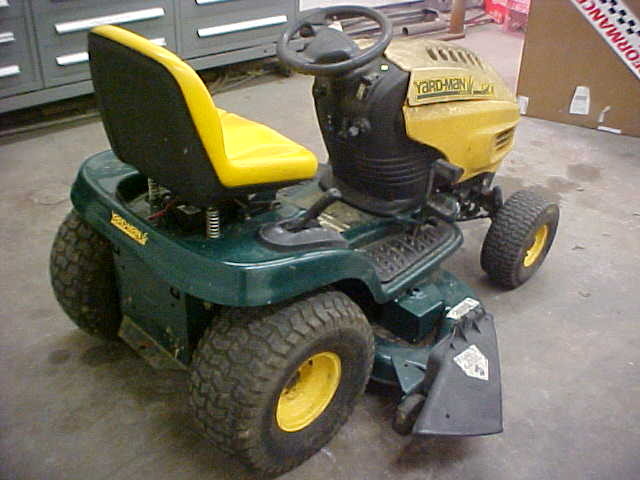
You'll be dealing with a vertical shaft motor as opposed to horizontal but to me, it's not a big deal. This one was extremely nice and with the advent of hydrostatic transmissions now, you can find some bigger motors on smaller mowers.
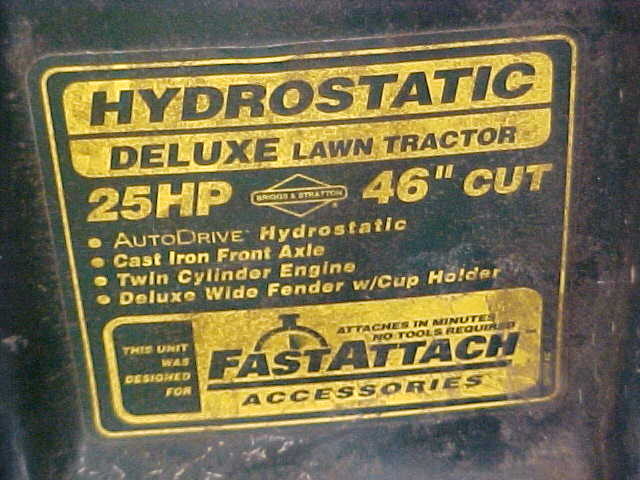
25 HP is more than I need for a 28 GPM pump but my thinking was with the way they label motors anymore, 25 HP today isn't what it used to be! Plus the fact if it wears some and the power decreases, I still have plenty to do what I want and it is not stressed

Only had 271 hours on it and got the mower for $325.00. Guy was moving and had to go. Found it on Craigslist. A big plus is you get a lot of extra stuff with a rider. I'll use this hour meter along with cables and such which will be nice.
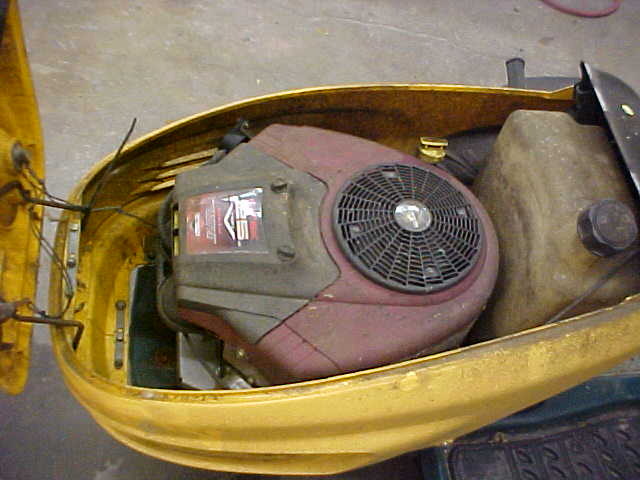
Ready to dig in! Ideally if you had a mower like this allready you could have a bunch of spare parts for your own. I'll sell the stuff off and you can basically get most, if not all, your money back. The electric clutch on this goes for $325.00. hydros are up there and decks are easy to resell in the Spring.
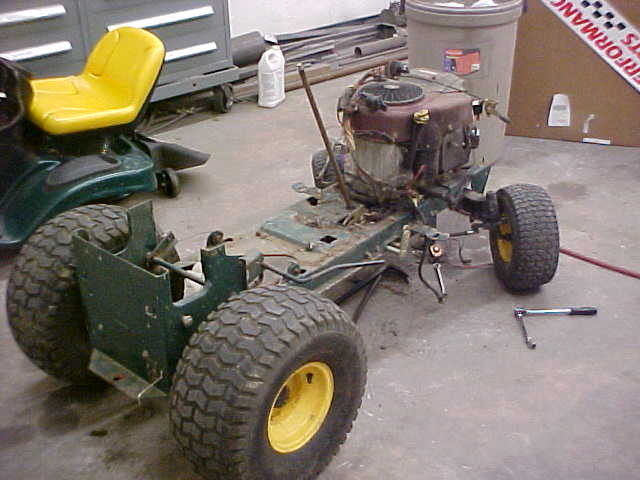
Less than a hour it was down to the motor. I didn't just rip stuff off as I labeled some of the safety stuff so when I go to clean up the wiring I know what to delete....hopefully!
(Side note) ended up selling all that I didn't want for $125.00 so I have $200.00 in the power plant and extras. Could have gotten more if I waited till the Spring but wanted it out of the way.
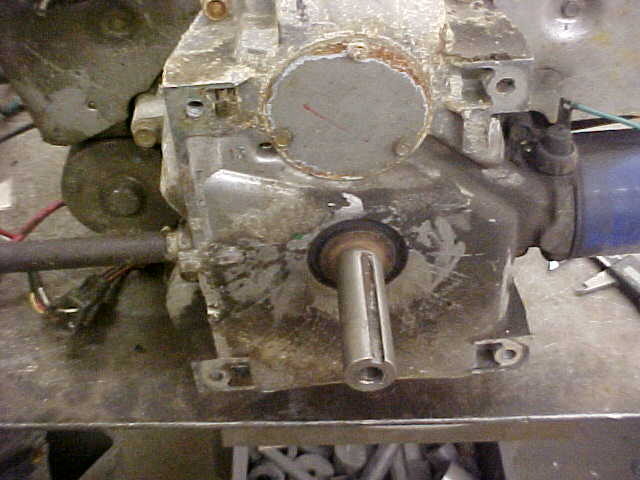
Electric clutch was easy to get off with impact as it's just 1 bolt. The pressed on pulley was a bear! Ended up welding to bolts with the heads cut off to the outside of it. Then ran that through a 1/2" plate and tightened the nuts. Old school trick but never failed me yet! No damage to the crank and you don't beat on it that way.
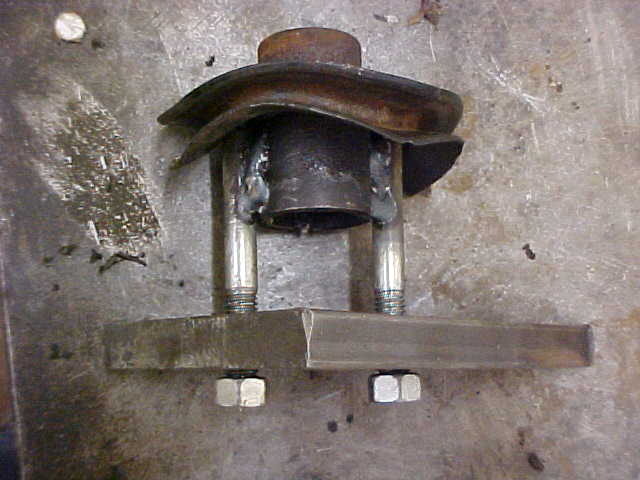
As you can see I tried the standard 3 jaw puller first and it was obvious that wasn't going to get it off. put washers to get more movement. I then loosened up and put a socket on the shaft and pulled it the rest of the way off.