I bought a 066 RL to rebuild that had the case broken off near the serial number, such that you could not bolt on a spike. I drilled and tapped 6x32 stainless screws into the case and formed up the area. I used the new spike, covered in blue masking tape as part of the form. I cast it with the bolt in it, also covered with tape. The entire area was sandblasted and cleaned with lacquer thinner prior to applying the JB Weld. This area is full of structural webbing. So with the JB Weld interlocking in all these pockets, in addition to the stainless screws, this repair should be very strong. What would you have done different?
Made good use of the old 084 badge.
Bolt still in it.
The spike removed.
A couple small air pockets got trapped behind the spike.
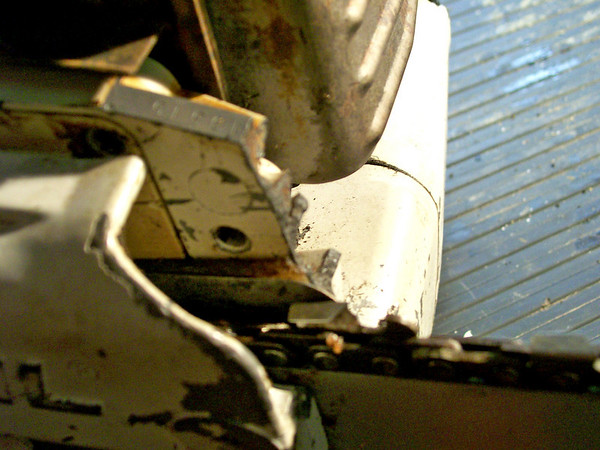

Made good use of the old 084 badge.
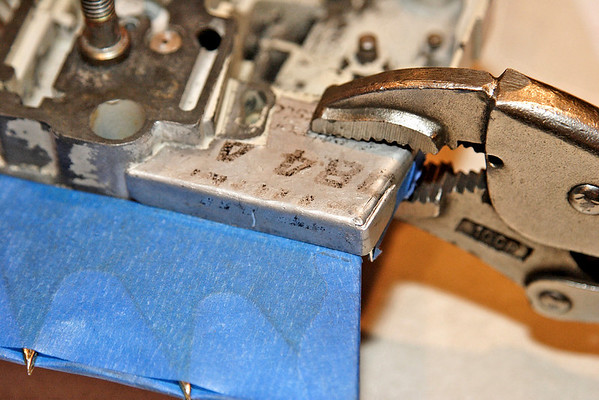
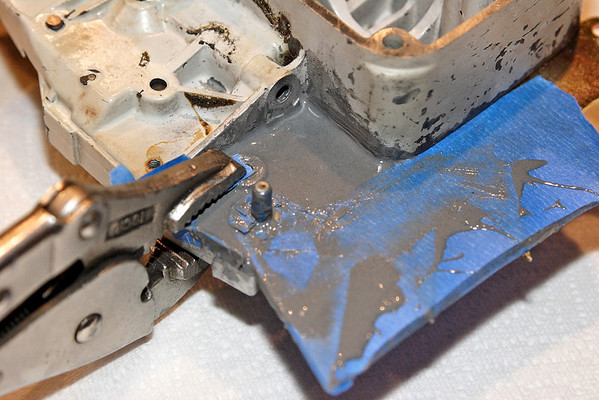
Bolt still in it.
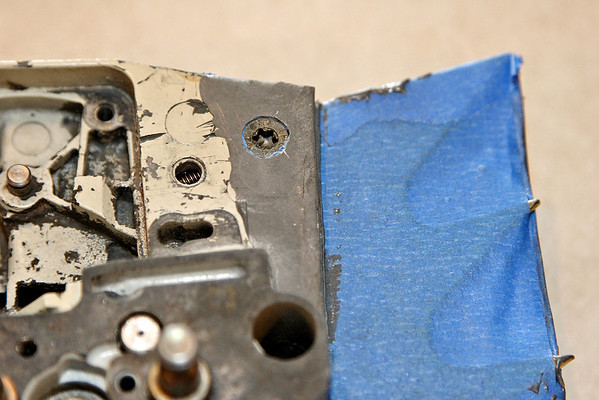
The spike removed.
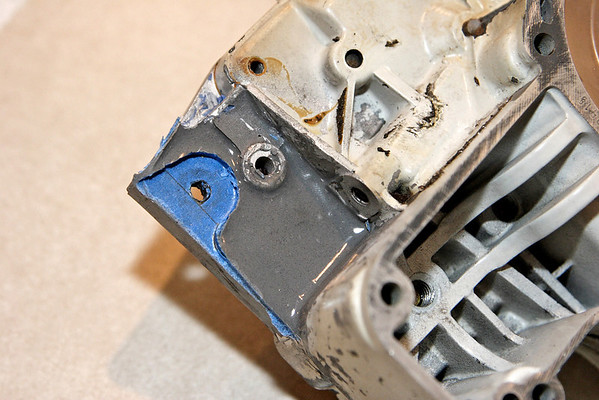
A couple small air pockets got trapped behind the spike.
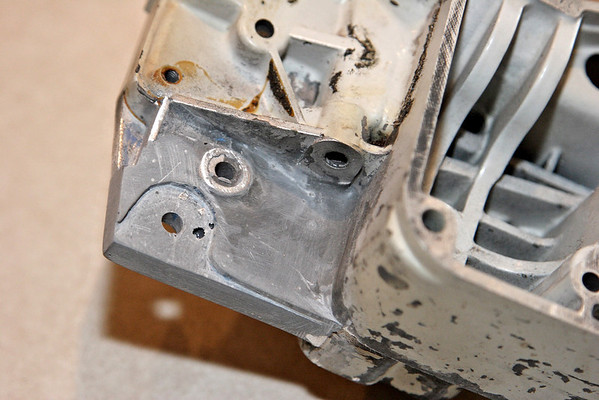

Last edited: