Started out like a fun conversion. Just slot some bolt holes they say, just grind a bolt they say.
Well tonight sucked. I slotted a bolt hole alright. 4 of them! Then I went to check squish so I could make a gasket. I am still a newbie to deep teardowns, but I had my calipers ready, and my daughter's play-doh wonderfully setup to measure squish. Well I (unwisely) installed the rings to do this. After having some trouble seating the rings, I decided to take them out and just get on to the next step so I could make the gasket tonight. Yeah, well I broke a ring.
1 ring down, I pressed on. Anyone got a ring for an 038 mag?? It's a meteor piston. PM me please!
Well, long story getting boring, here's what I found. The mag cylinder base won't sit flush. There is a ridge running along the outside edge (exhaust to intake direction) that prevents the cylinder from bottoming out. Thoughts on how to move forward?
Well tonight sucked. I slotted a bolt hole alright. 4 of them! Then I went to check squish so I could make a gasket. I am still a newbie to deep teardowns, but I had my calipers ready, and my daughter's play-doh wonderfully setup to measure squish. Well I (unwisely) installed the rings to do this. After having some trouble seating the rings, I decided to take them out and just get on to the next step so I could make the gasket tonight. Yeah, well I broke a ring.
1 ring down, I pressed on. Anyone got a ring for an 038 mag?? It's a meteor piston. PM me please!
Well, long story getting boring, here's what I found. The mag cylinder base won't sit flush. There is a ridge running along the outside edge (exhaust to intake direction) that prevents the cylinder from bottoming out. Thoughts on how to move forward?
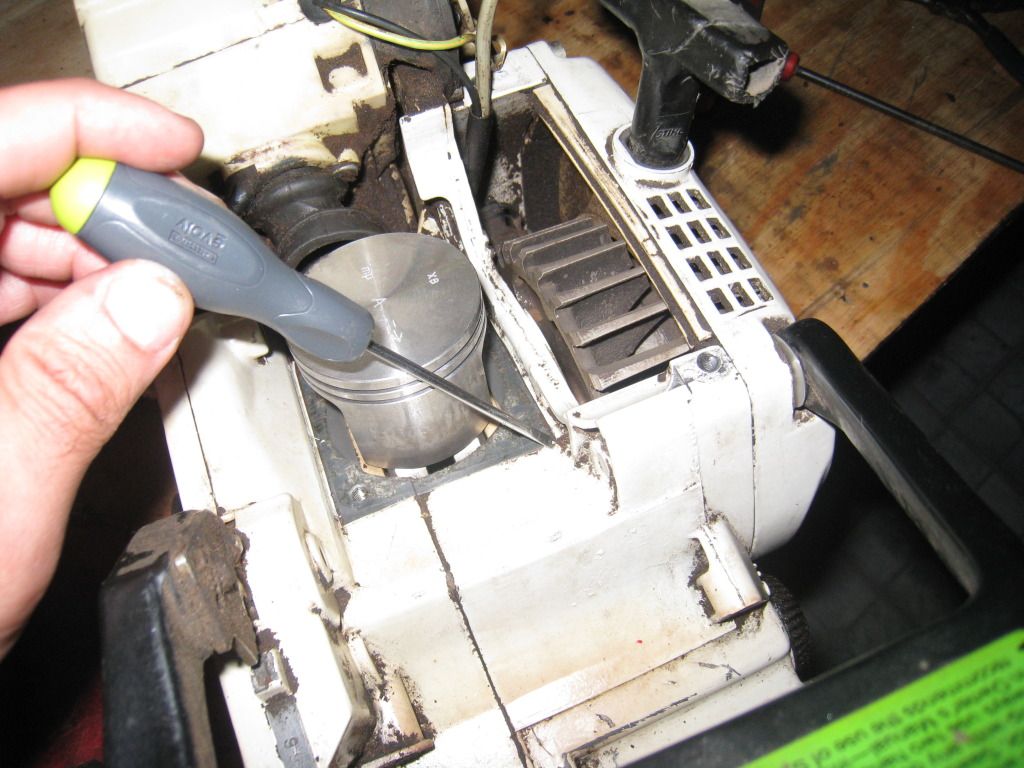
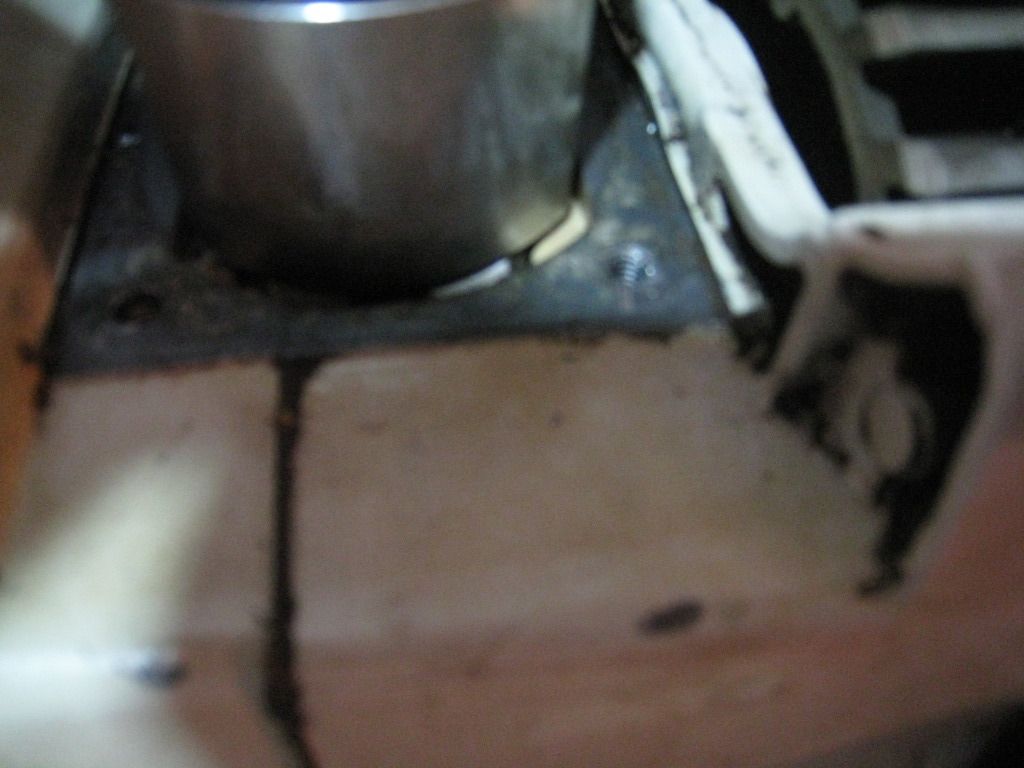
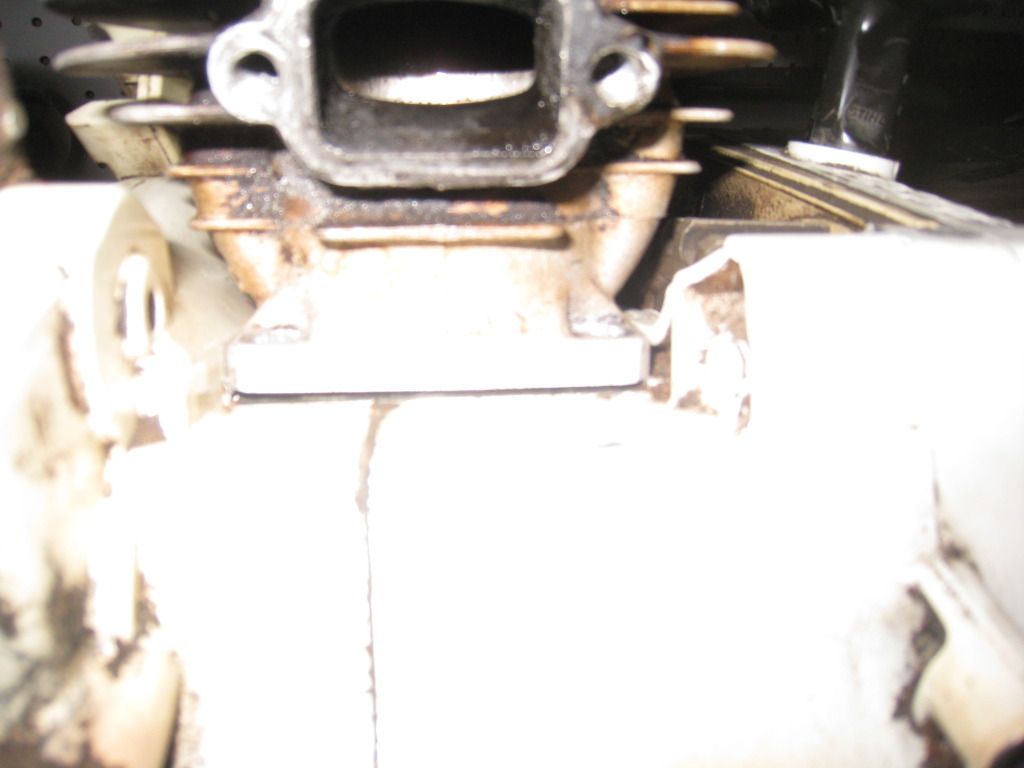
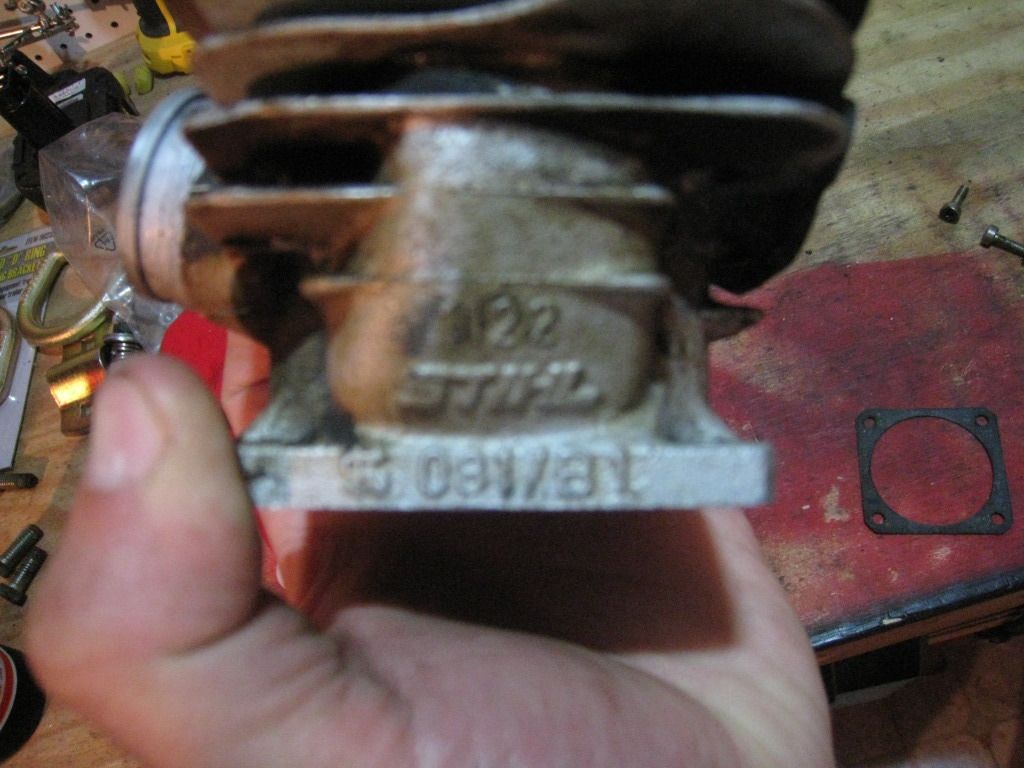