Stumpys Customs
Stumpbroke
I know this has been done before, but with the search bein the way it is I though I'd start a new thread. I'll go through how I set up & read a degree wheel. The saw it's on is a Husky 576xp without the base gasket installed.
I bought a 1/2' drill chuck from Harbor freight to mount to my wheel.
Find a suitable place to mount the pointer.
I bought a 1/2' drill chuck from Harbor freight to mount to my wheel.
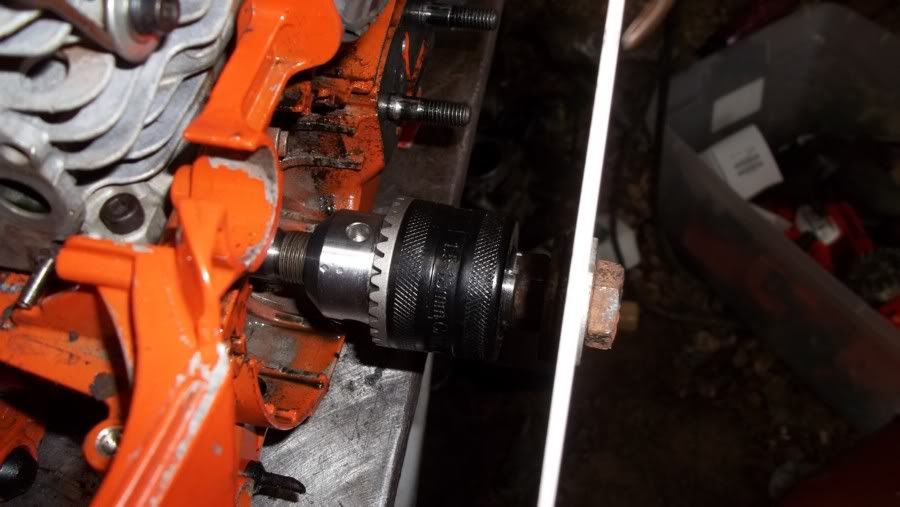
Find a suitable place to mount the pointer.
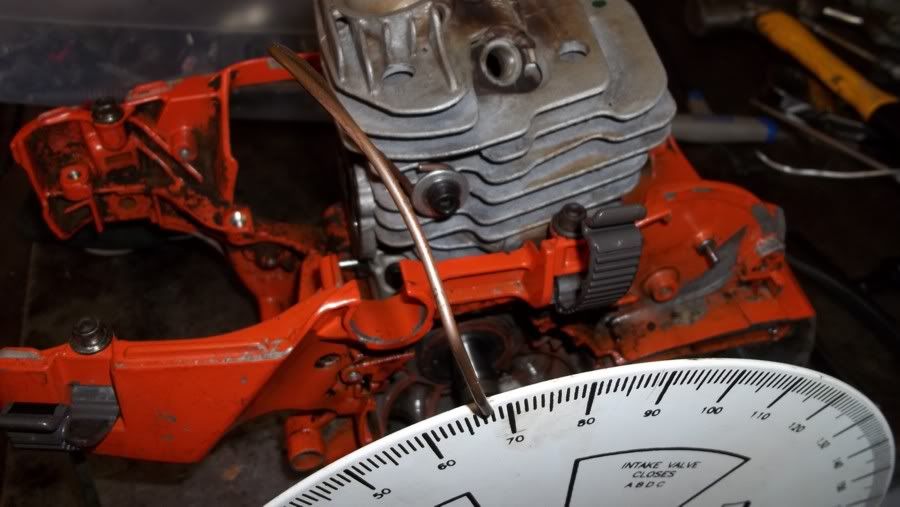
Last edited by a moderator: