So you've got a Husky with a muffler that shakes rattles and rolls? You know what I'm talking about, a 350. Or similar variant that may have the same problem. Now we all know theres a new revised muffler out there that's been reengineered to prevent this problem from happening again, but few want to spend the coin on it. Tried the helicoils have you and they're just not holding up? Loctite just a little too permanent for ya? Well there's a good solid solution that just takes a little patience and a few tools. I was able to do this without pulling the jug, and this was actually on a 353 that had been tampered with someplace else then given back to the customer in a box 'o' parts. The cylinder threads were gone except maybe a couple in the back.
This idea was a collective effort, I certainly can not take full credit. I had to pick spike60's brain (there's a lot in that thing!) for ideas. I was going to use exhaust studs from a Jonny 670 but they're just too short. That would only have required tapping the cylinder, the studs are 6mm cylinder end and 5mm muffler end. So I told him my dilemma and what I was trying to do. He popped out the knowledge that the 288 bolts were bigger and possibly longer.... And he was right! Couldn't be happier with the quick, easy, and clean results.
Here's what you need:
1/4" drill bit
13/64" drill bit
(2) 288XP muffler bolts
6mm x 1.00 metric tap
Drill
Vise or other clamping device
Small ViseGrips or locking pliers
Remove the muffler from the cylinder (if this isn't already done)
Place muffler in vise with access to bolt holes.
With 1/4" drill bit, slowly and carefully drill out the holes. Use of WD40 or some type of drilling/cutting oil will help keep things cool and clean.
Extremely slowly and carefully drill out holes in gasket. Too fast and she'll snap, they're brittle under these circumstances.
Drill out the heat shield.
If applicable, drill out the muffler brace.
With 13/64" drill bit, drill out bolt holes in cylinder. I recommend covering or stuffing the exhaust port to prevent shavings from entering.
Use the 6mm tap to tap the holes, preferably with some WD40 or other oil. I used ViceGrips to do this, standard tap tools typically won't fit. I did have to loosen the bucking spike and tilt it forward to be able to work the cylinder.
You are all done! Reassemble exhaust components using the 288XP muffler bolts and get cutting!
This idea was a collective effort, I certainly can not take full credit. I had to pick spike60's brain (there's a lot in that thing!) for ideas. I was going to use exhaust studs from a Jonny 670 but they're just too short. That would only have required tapping the cylinder, the studs are 6mm cylinder end and 5mm muffler end. So I told him my dilemma and what I was trying to do. He popped out the knowledge that the 288 bolts were bigger and possibly longer.... And he was right! Couldn't be happier with the quick, easy, and clean results.
Here's what you need:
1/4" drill bit
13/64" drill bit
(2) 288XP muffler bolts
6mm x 1.00 metric tap
Drill
Vise or other clamping device
Small ViseGrips or locking pliers
Remove the muffler from the cylinder (if this isn't already done)
Place muffler in vise with access to bolt holes.
With 1/4" drill bit, slowly and carefully drill out the holes. Use of WD40 or some type of drilling/cutting oil will help keep things cool and clean.
Extremely slowly and carefully drill out holes in gasket. Too fast and she'll snap, they're brittle under these circumstances.
Drill out the heat shield.
If applicable, drill out the muffler brace.
With 13/64" drill bit, drill out bolt holes in cylinder. I recommend covering or stuffing the exhaust port to prevent shavings from entering.
Use the 6mm tap to tap the holes, preferably with some WD40 or other oil. I used ViceGrips to do this, standard tap tools typically won't fit. I did have to loosen the bucking spike and tilt it forward to be able to work the cylinder.
You are all done! Reassemble exhaust components using the 288XP muffler bolts and get cutting!

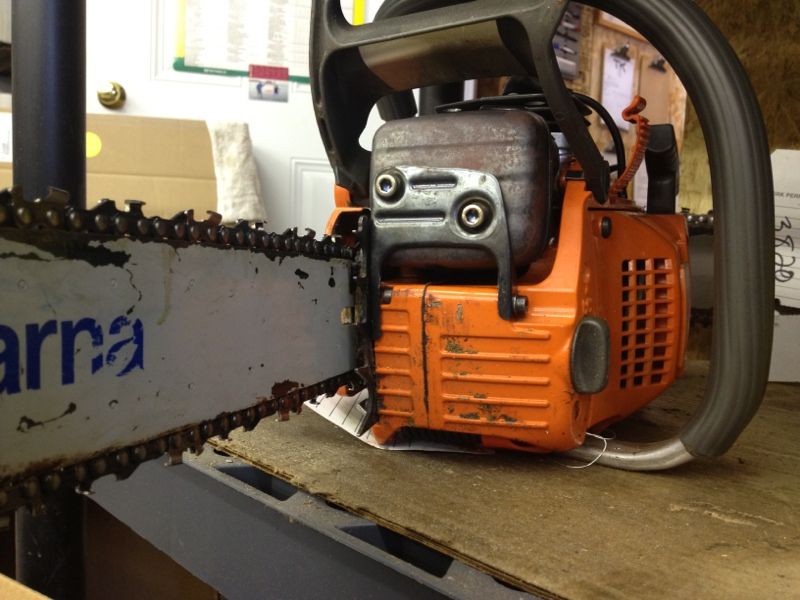