jgrady1982
ArboristSite Lurker
Hello,
I am requesting the help of all of the local chainsaw experts. I am rebuilding an 028WB and tonight I installed the crank seals. I read all last night about packing them with grease and then seting them level with the case.
I ended up using plain red wheel bearing grease and a deep well socket.
Does this look correct? The seal on the clutch side is set down to level with the case and then the outer (more towards me) part of the seal lip kind of rolls over a portion of the crankshaft. Is this normal? Or should I use a dental pick and push that portion of the seal down (toward the bearing) so that it is not "rounded" over that portion of the crankshaft.
Here are the pics:
This is the larger seal packed with the red wheel bearing grease.
The two seals together.
A (okay) pic of the seal with the end of the seal wrapped around the "shoulder" on the crankshaft.
I am requesting the help of all of the local chainsaw experts. I am rebuilding an 028WB and tonight I installed the crank seals. I read all last night about packing them with grease and then seting them level with the case.
I ended up using plain red wheel bearing grease and a deep well socket.
Does this look correct? The seal on the clutch side is set down to level with the case and then the outer (more towards me) part of the seal lip kind of rolls over a portion of the crankshaft. Is this normal? Or should I use a dental pick and push that portion of the seal down (toward the bearing) so that it is not "rounded" over that portion of the crankshaft.
Here are the pics:
This is the larger seal packed with the red wheel bearing grease.
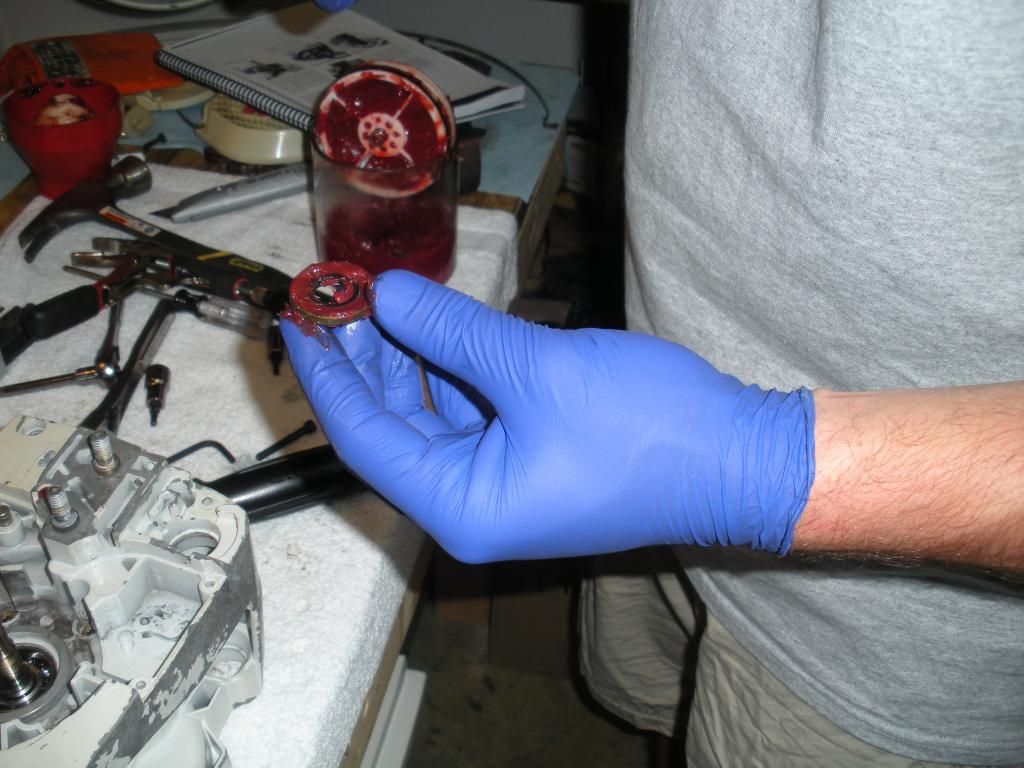
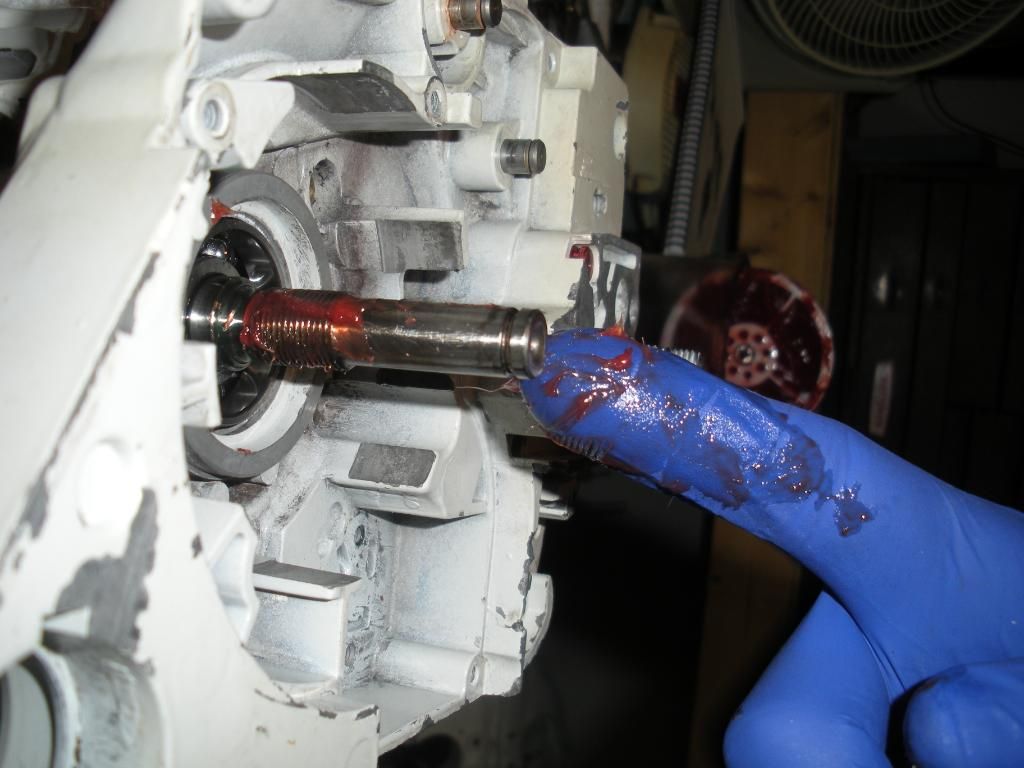
The two seals together.
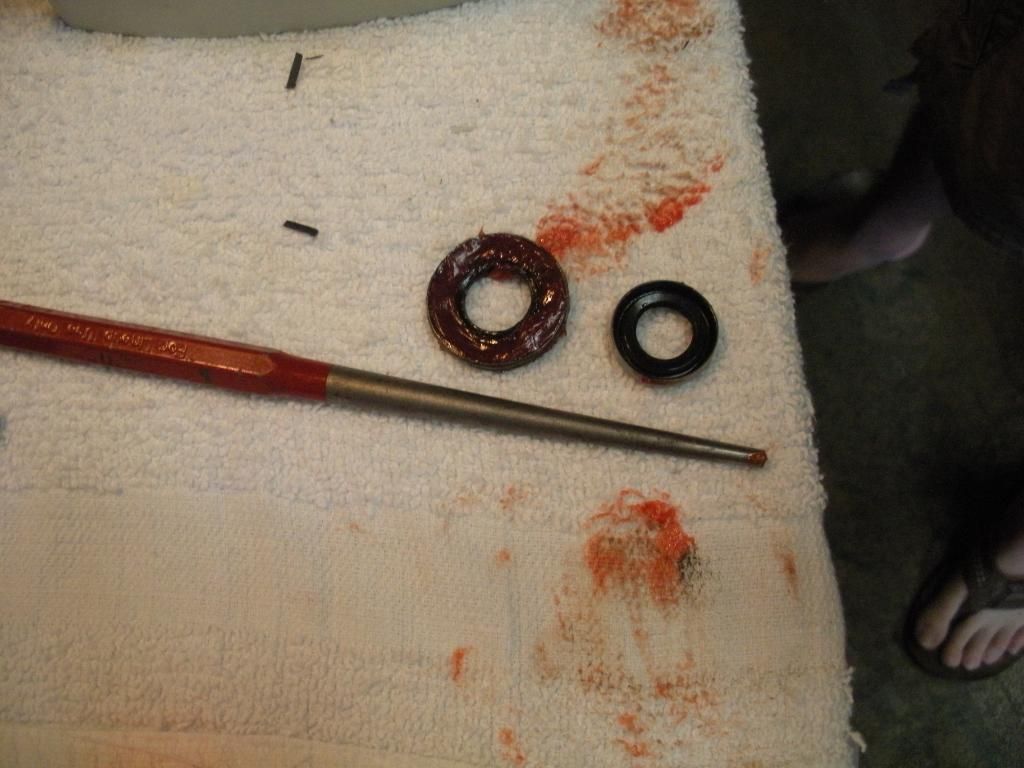
A (okay) pic of the seal with the end of the seal wrapped around the "shoulder" on the crankshaft.
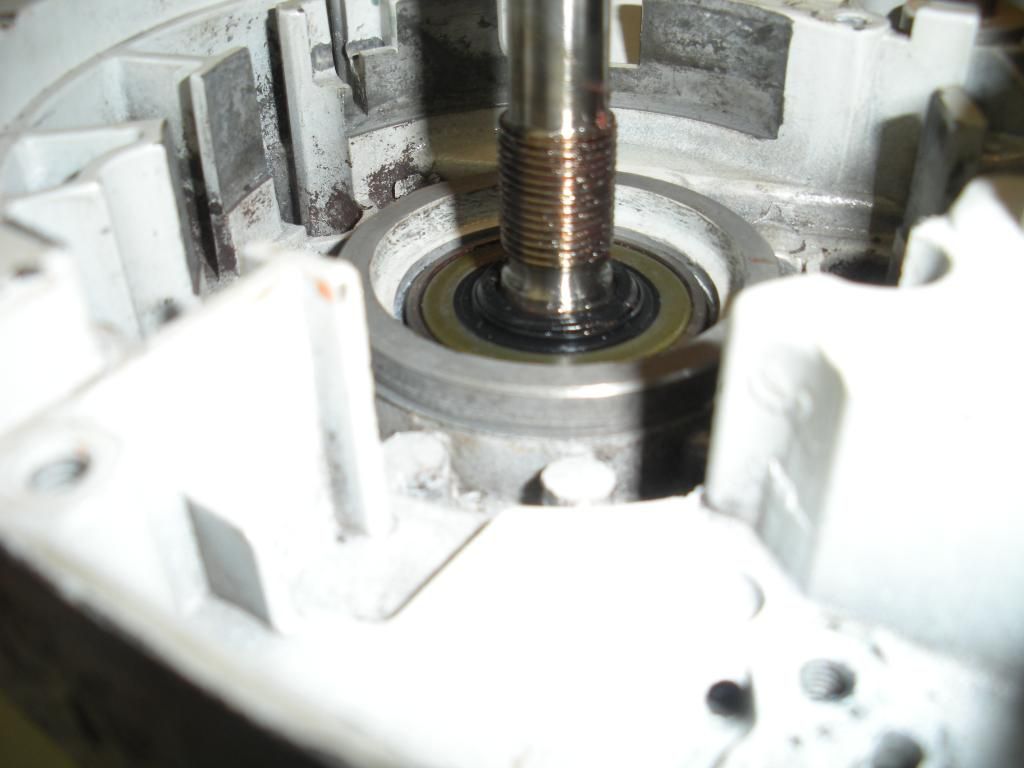
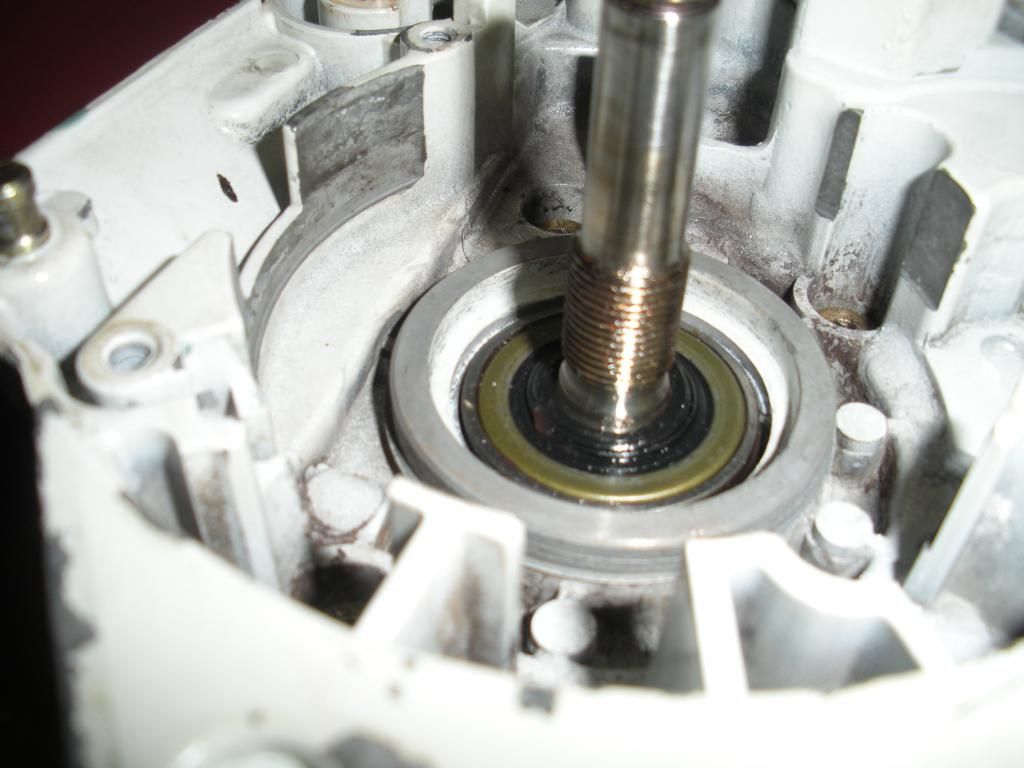
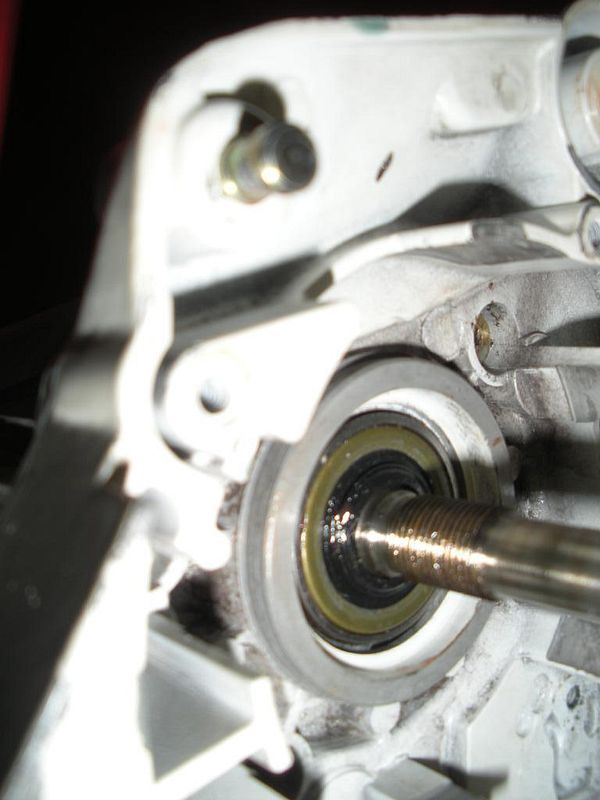
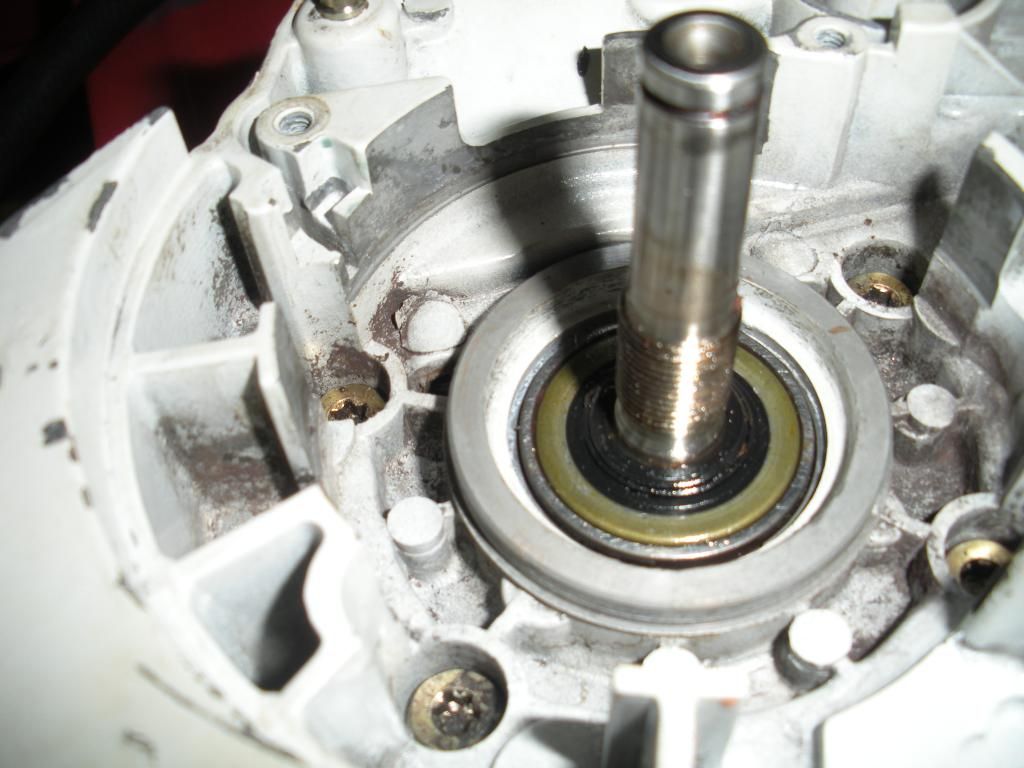