Nuzzy
Trail Gnome
We're in our slow(er) season at work which means I get more time to play around with projects I've been meaning to do. Got the log arch pretty much done, but carrying all my gear into the woods was a pain. Something HAD to be done!
So tonight I made this
It sits atop of my adjusty hitch (so I could keep it inboard more so than all hanging out the back), and stores everything I need when I head into the woods. Saw box, fuel, oil, mingo, various chains and shackles, big and little saws, etc.
It's out of the way and high enough that it wont interfere with the tight turning of the log arch, and should securely hold everything in place through uneven terrain. The saws are held on with gnarly screws and fender washers so hopefully they'll stay put!
I can't wait to get out in the woods this weekend!!


So tonight I made this
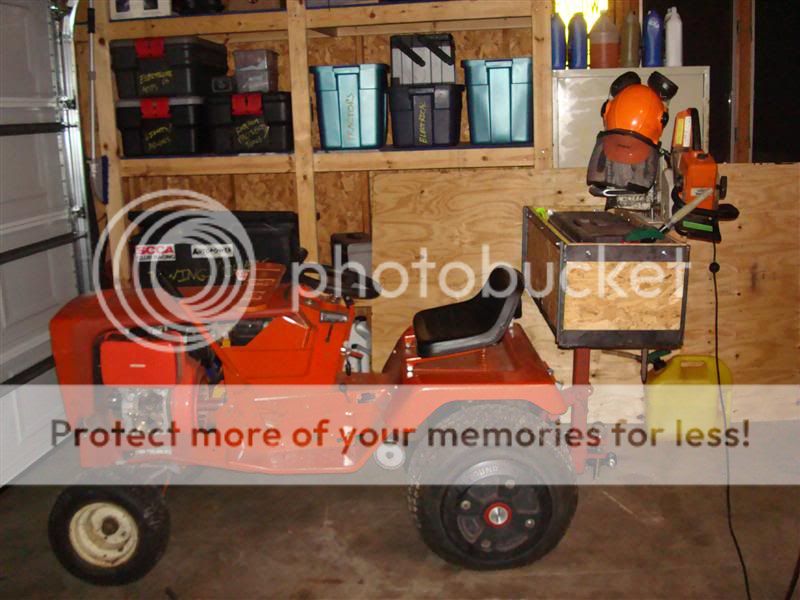
It sits atop of my adjusty hitch (so I could keep it inboard more so than all hanging out the back), and stores everything I need when I head into the woods. Saw box, fuel, oil, mingo, various chains and shackles, big and little saws, etc.
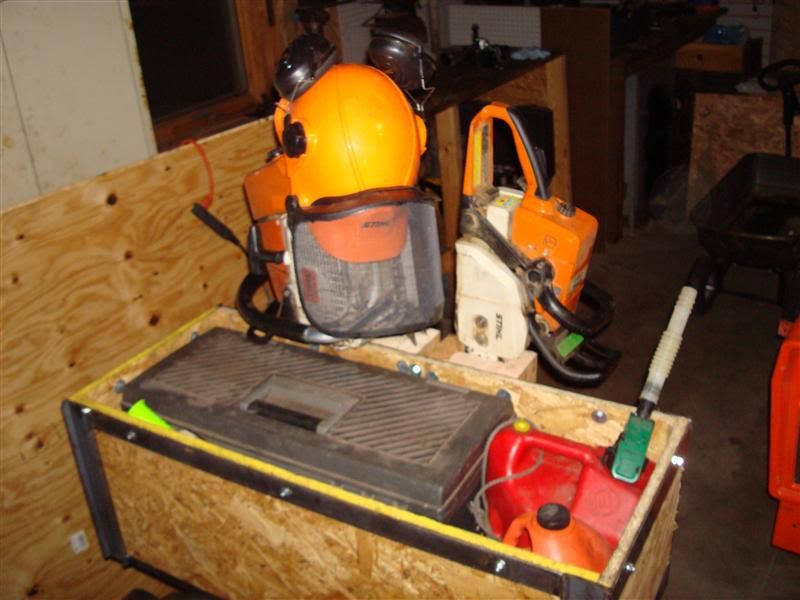
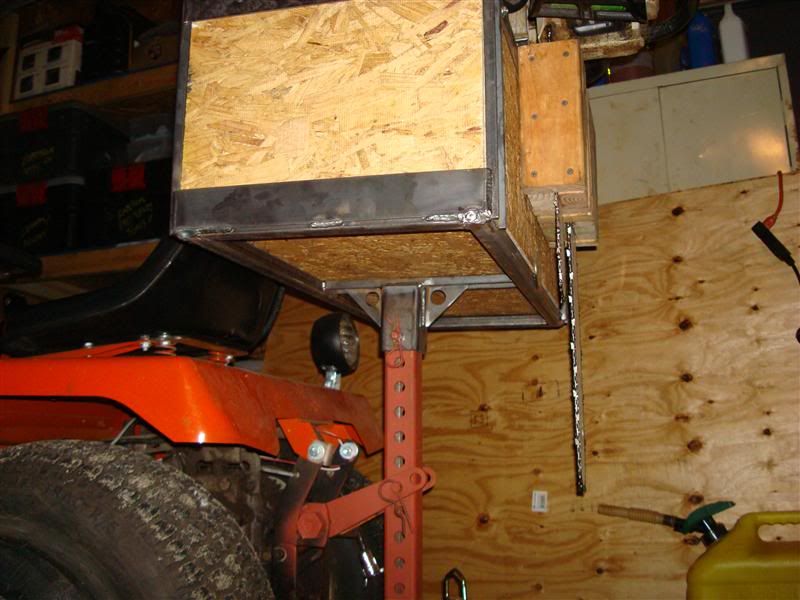

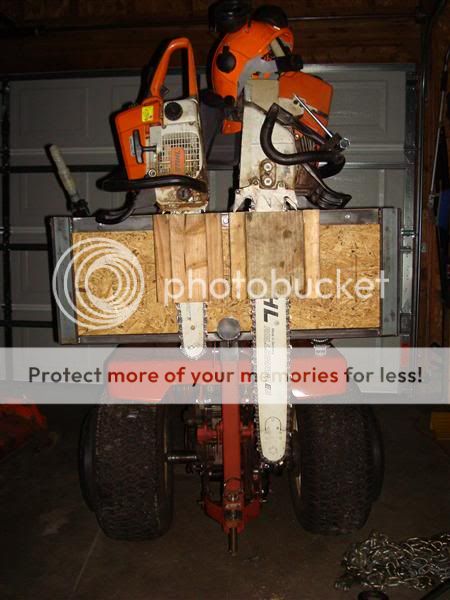
It's out of the way and high enough that it wont interfere with the tight turning of the log arch, and should securely hold everything in place through uneven terrain. The saws are held on with gnarly screws and fender washers so hopefully they'll stay put!
I can't wait to get out in the woods this weekend!!


