Thanks Shaun.
Here's where Mike was a few days ago with the parts.
Here's where Mike was a few days ago with the parts.
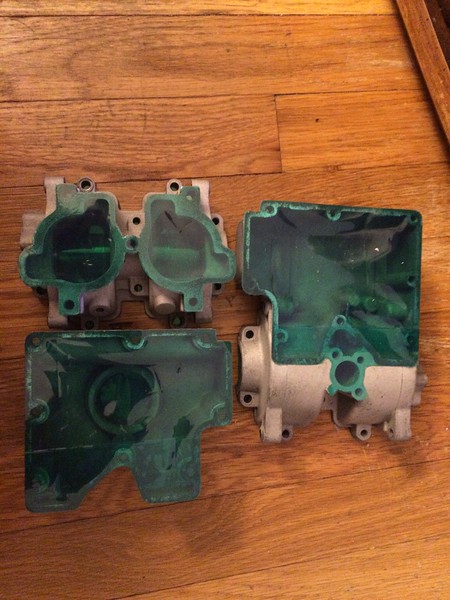
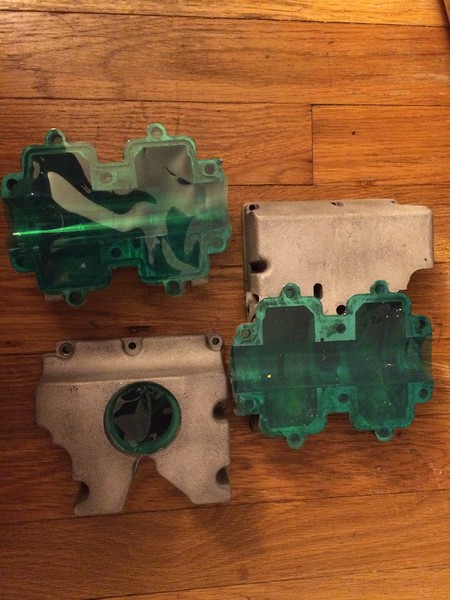
I'll fill the pores as soon as I get it back and get it headed your way. Hopefully you'll have it next week.Brad any idea when the other piece is returning
Trimix is for stainless MIG. Helium straight or added to Argon is for DCEN aluminum (pure He) or for thicker aluminum than can be done with the Amps you're using.Is it it feasible or even doable to run a hot pass or two, no filler rod, just arc only
and see if the metal finishes out-gassing the contaminates?
Odd as it might seem, we had some repair work on greasy carbon steel
(With No information about what additive package any of the lubes had carried)
and couldn't seem to cook it off with taking it orange heat w/oxy-acetylene
and letting it cool to room temp/bare hand pick-it-up temps.
Something in the back of my head said try running a quick thin pass at a slightly
over volted/hot setting of the mig gun.
That seemed to do the the trick! A bit of cleaning the slightly funky looking specks of slag/scale, light kiss with the sander,
and you were ready to tig on the repair bits.
I never had any chance to try my hand at welding Magnesium..
Got fairly comfortable with the occasional aluminum parts that came through the shop [ probably 60xx alloy mostly]
( counting owner, we were about a 6~8 man, jobshop-machining/fabrication co.)
The power supply was a Lincoln Idealarc 300, so no options for trying any interesting waveforms or duty cycles of them etc.
sheesh that's been a long time, nowdays I cant even recall the percentages of the tri-mix
gas we generally ran on the mig rig [ CO2/Argon/Helium ] Makes for way less spatter.
When metal is heated to a neutral or aneahile state and a cleaning gas is introduced this is truly the easiest way to clean metal or remove debris. BTW Shaun did not do a good job but an amazing he is truly in the top of his field. Some people just have the knack for it. I am jealous of people that just get it. I had to put a ton of practice to get as good as I am but I guess that just makes me appreciate it more. [emoji57]Is it it feasible or even doable to run a hot pass or two, no filler rod, just arc only
and see if the metal finishes out-gassing the contaminates?
Odd as it might seem, we had some repair work on greasy carbon steel
(With No information about what additive package any of the lubes had carried)
and couldn't seem to cook it off with taking it orange heat w/oxy-acetylene
and letting it cool to room temp/bare hand pick-it-up temps.
Something in the back of my head said try running a quick thin pass at a slightly
over volted/hot setting of the mig gun.
That seemed to do the the trick! A bit of cleaning the slightly funky looking specks of slag/scale, light kiss with the sander,
and you were ready to tig on the repair bits.
I never had any chance to try my hand at welding Magnesium..
Got fairly comfortable with the occasional aluminum parts that came through the shop [ probably 60xx alloy mostly]
( counting owner, we were about a 6~8 man, jobshop-machining/fabrication co.)
The power supply was a Lincoln Idealarc 300, so no options for trying any interesting waveforms or duty cycles of them etc.
sheesh that's been a long time, nowdays I cant even recall the percentages of the tri-mix
gas we generally ran on the mig rig [ CO2/Argon/Helium ] Makes for way less spatter.
Even if i get these parts done we can do this part even if the others are done just send back all together
Sent from my iPhone using Tapatalk
Nice job Srcarr.
I see what you mean about Mag welding. Looks ALOT more forgiving than Aluminum.
So pretty much you use the laywire technique on AC?
Which filler rod and how many did you use?
The grinding and shaping look harder than the welding, but then again, that's what happens when you watch anyone whose good at it.
Is it it feasible or even doable to run a hot pass or two, no filler rod, just arc only
and see if the metal finishes out-gassing the contaminates?