I put that sheet on that table after I built the shop and figured I redo it if the height needed adjustment or something. Never did, so I guess it's okay. LOL Be nice to have a clamping table but there are ways around it. I'm not a production shop and mainly just do my own projects and repairs.I like your welding table and the saw. I need to take pictures of mine (table and shelf queen's 090 and 075.) My welding table is quite similar. the top is a bit thicker and it has holes bored in the ends for TIG torch storage ( when using them) and mine is very heavy and on 'borrowed from a Ford assembly plant neoprene tired casters too (care of my BIL). and his lunch box. Mine weighs in at about 1000 pounds, give or take. Welders aren't. Just sold my Lincoln Square Wave TIG and my Hypertherm 85 amp plasma. Replaced them with 2 much lighter and way more efficient (electric consumption wise) solid state machines. Have a plasma table as well, A Langmuir that I'm about to upgrade to a full sized Shop Saber.
I'm still using a Hypertherm 1100 I bought new.
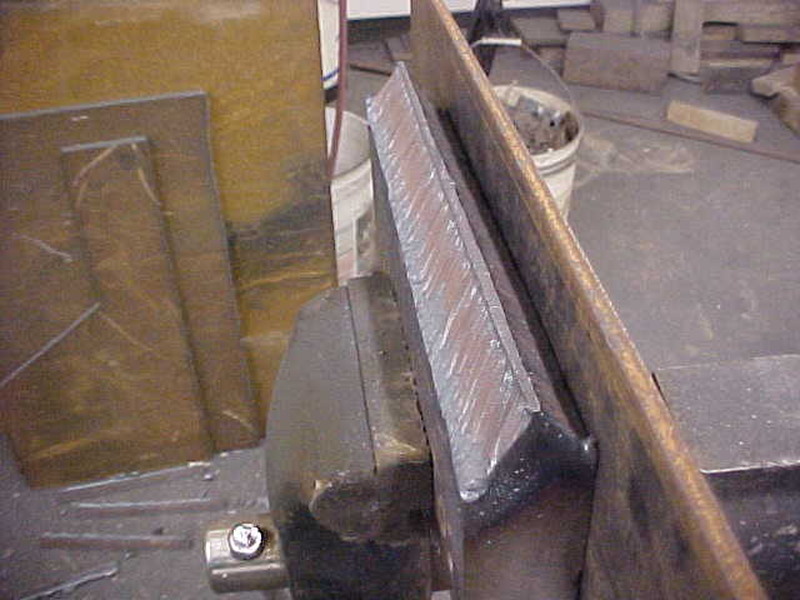
I was pretty disappointed with the company when I found out why they offered me an "upgraded" torch lead for a slight discount weeks after purchase. My torch died about 6 years later and dealer's repairman let it slip. He told me I must have been very careful with mine as nearly every one died within a year as they had a Major flaw in them. Instead of Hypertherm fessing up to it, they wanted you to pay extra for their mistake. Over a grand as you had to replace the WHOLE torch lead length. I naturally had a long length.
It would be awesome to get a table with a CNC driver.
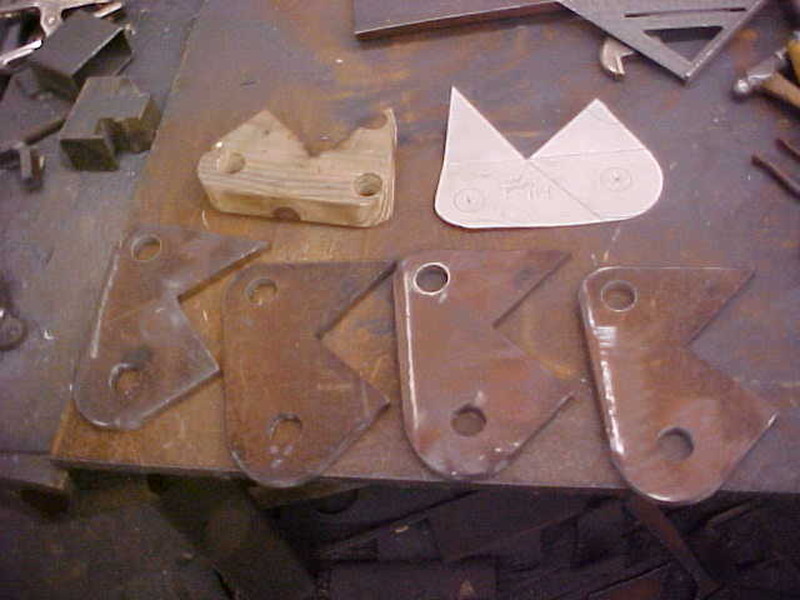
I do it old school and make wood tracer patterns if I want stuff the same. Drill the holes and use that as locators, then cut the outer.
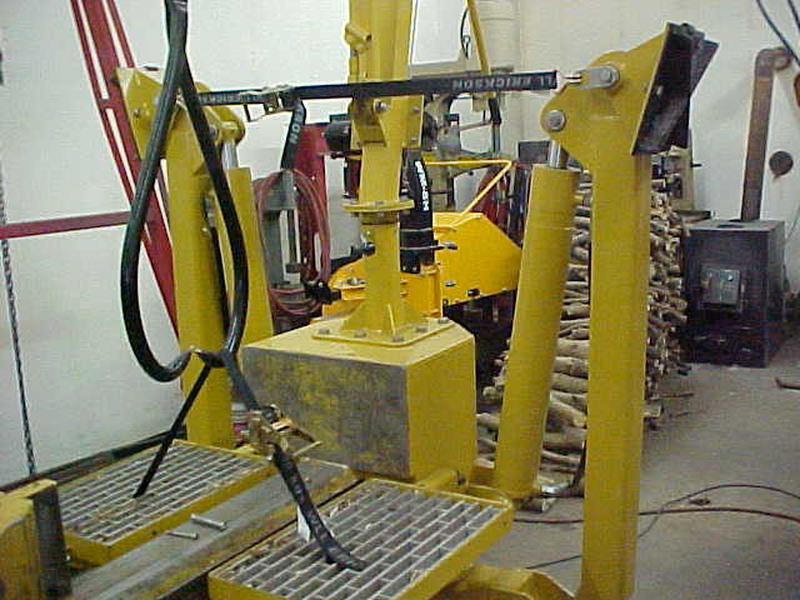
Takes a little time but worth it to me.