Opihi59
ArboristSite Operative
I just installed one of these today. On a Craftsman 2300CVA. It worked, thank goodness. Finally, oil to the bar. This thread helped. Thanks.
Glad it helped you. So I put some motor oil 10W-30 in and cranked it up. Let it idle a bit and then went to a fast idle. I did not have bar/clutch etc on it so I could watch the satisfying oil flow.
NOT.
I didn't get any oil output. Now I did check my other checkvalve/pump inside the oil tank, and remember that I was able to suck thru it but not blow which tells me that part of the system works. I have a few more thoughts on the system, as I am finding it pretty simple overall, but just frustrating. So here is a photo with some labels. The blue arrow points to the opening into the oil tank, the green arrow points to where the oil comes out of course, well, at least where it is supposed to come out.
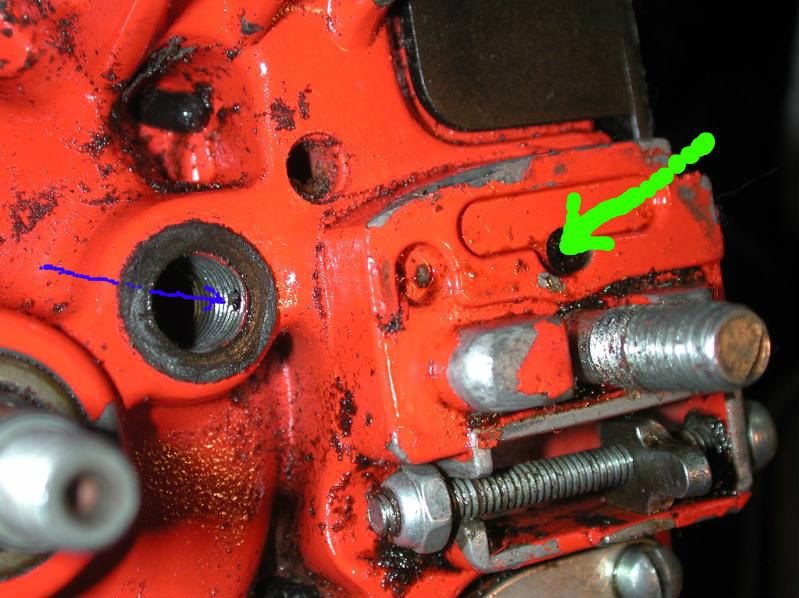
I ran a pipe cleaner thru this hole, and it passes unobstructed into the oil tank. The check valve has entry of crankcase pulse pressure in thru the end with the mesh wire, and the pressure then comes out the hole near the head of the check valve, as shown below.
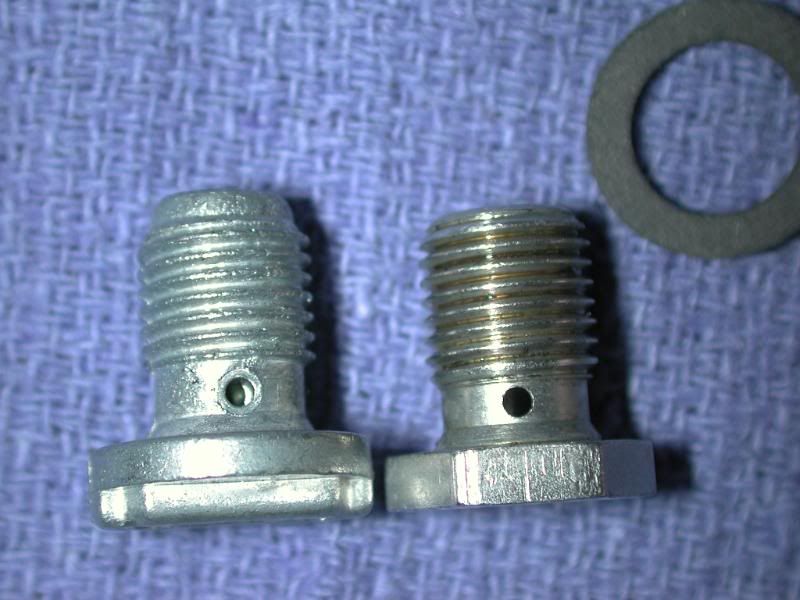
It is not necessary for the hole below the head to line up with the hole into the oil tank--the tapered/conical base of the check valve just below the head seals the outside, and pulse pressure is fed from the crankcase one-way into the circular donut area between the uppermost threads and the base of the head-and then it goes into the tank thru the little side hole in the case. In this interpretation the hole in the check valve does not have to line up in any way with the hole in the case, and in fact, it doesn't in my original, or in the replacement; it ends up in about the 6 O'clock position indicated by the blue arrow in the photo below where I made a small indexing scratch on the head.
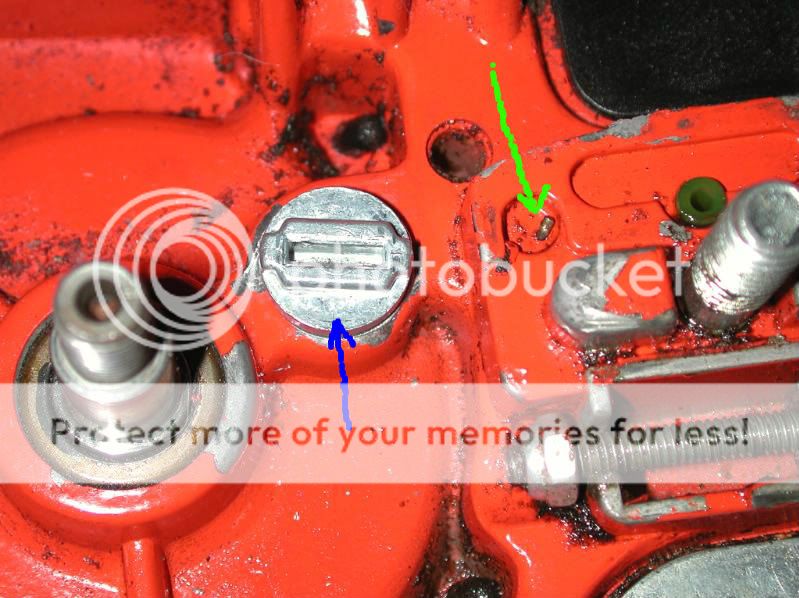
So now everyone is wondering what the green arrow is pointing at in the photo above...me too. This is a small bent piece of wire, that freely spins around in that dimple. When I put some oil over it while the saw was running, I got a few bubbles. I'm not sure of its purpose so if anyone else is, let me in on that secret. I am convinced that all is right with my oiler system, it just doesn't oil out the hole. I did run a pipecleaner into the oiler line, it is not pinched in any way and it is new from the original line. It isn't folded over and obstructed on the inside of the oil tank. It is possible I had low oil with just about 3 oz in the tank so it didn't build up enough pressure in there to start moving oil, and this may have been compounded by there not being enough RPM load on the motor to produce adequate pressure in the system to make it push oil out. I am really not sure. And that little wire thingey at the green arrow has me a bit confused as to its purpose, is it merely a safety to prevent the oil tank over pressurizing? Dunno. I know I have a tight cap on the tank, it isn't leaking and makes a good seal. Despite the new check valve, is pressure leaking back into the crank case around the threads, and should I teflon tape those and re-install it? I will have to mess with this more some other time, but for now, I'll just sit on it.